Superior vacuum insulation in stainless steel bottles requires meticulous surface preparation, proper outgassing, strategic getter material placement, and flawless sealing techniques. These critical manufacturing steps ensure long-term thermal performance, not just initial testing results that many manufacturers showcase.
As a manufacturer with over a decade of experience producing premium vacuum-insulated bottles, I've seen firsthand how proper vacuum technology makes all the difference. Let me take you behind the scenes of what truly matters in vacuum insulation manufacturing, beyond the marketing claims you typically hear.
Proper manufacturing steps ensure long-term insulation performanceTrue
Meticulous surface prep, outgassing, getter placement, and sealing are critical for lasting vacuum insulation.
Stainless steel bottles have perfect vacuum insulation by defaultFalse
Manufacturers can cut corners in the manufacturing process, leading to loss of insulation over time.
How is superior vacuum insulation actually achieved in stainless steel bottles, beyond the marketing claims
Most buyers focus only on initial thermal tests, but they're missing what really matters. The true performance of vacuum insulation reveals itself months after purchase, when inferior products begin failing while premium bottles maintain their performance.
Achieving superior vacuum insulation requires four critical elements: meticulous pre-vacuum surface preparation, proper outgassing through high-temperature baking, strategic placement of getter materials to absorb residual gases, and flawless final sealing techniques that maintain vacuum integrity for years.
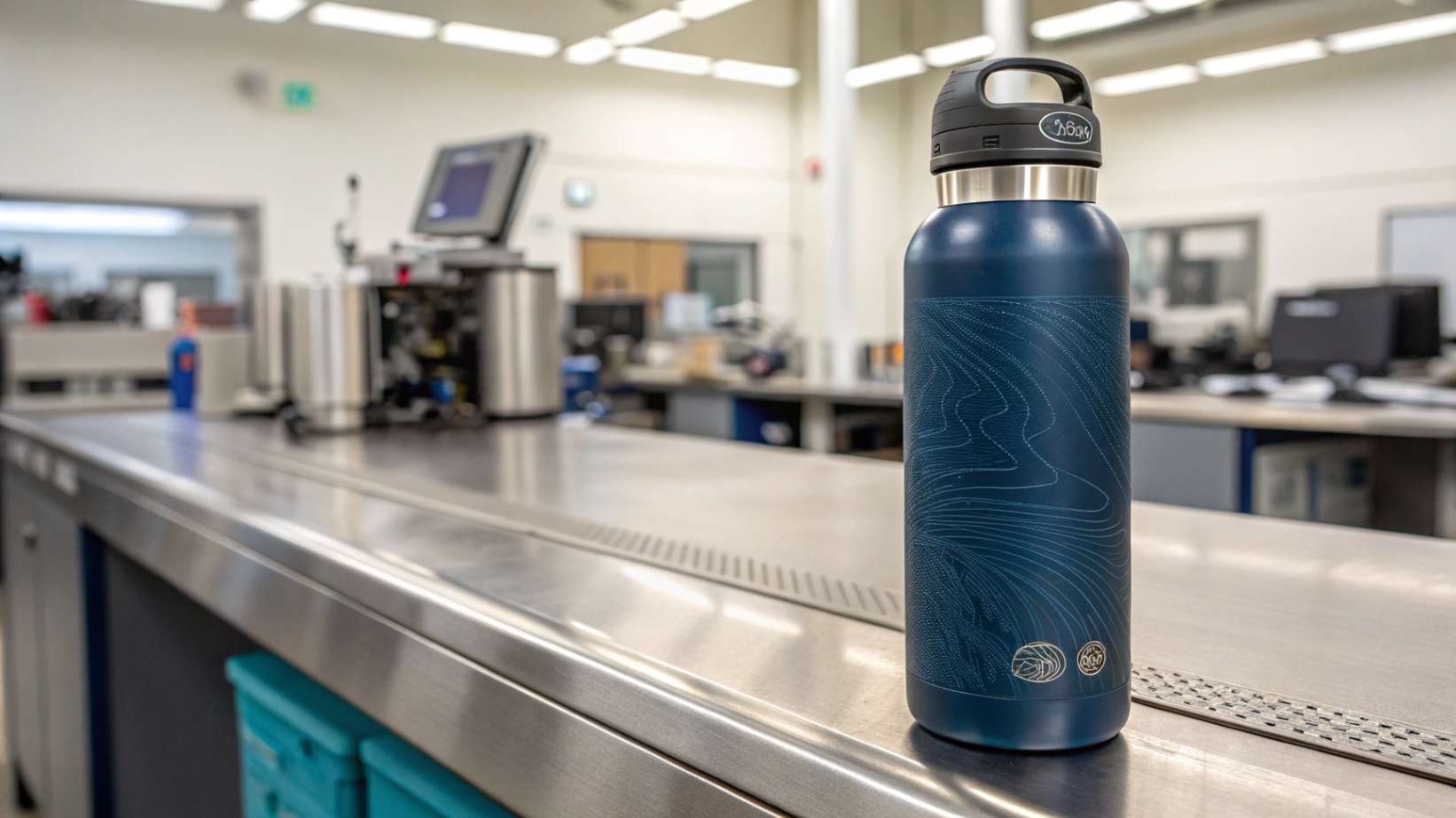
The Foundation: Surface Preparation and Outgassing
The journey to exceptional vacuum insulation begins long before the vacuum pump is connected. At Cupique, we've invested heavily in surface preparation because we know it's the foundation of lasting performance.
Pre-vacuum surface preparation isn't just about cleaning—it's about creating the perfect environment for a stable vacuum. This involves:
- Thorough Degreasing: We use specialized solvents and ultrasonic cleaning to remove all traces of oils and manufacturing residues.
- Outgassing Process: Our stainless steel components undergo baking in vacuum furnaces at temperatures between 300-500°C for several hours.
This critical outgassing step removes adsorbed water vapor, oils, and volatile organic compounds from the stainless steel surfaces. Without proper outgassing, these contaminants will slowly release into the vacuum cavity after sealing, gradually degrading insulation performance.
The Unsung Hero: Getter Materials
One element rarely discussed in marketing materials is the use of getter materials:
Getter Type | Composition | Benefits | Typical Applications |
---|---|---|---|
Barium-based | Pure barium or alloys | Excellent for adsorbing nitrogen, oxygen | Premium bottles |
Zirconium alloys | Zr-V-Fe combinations | Broad spectrum gas adsorption | High-performance models |
Non-evaporable getters | Sintered metal powders | Long-term stability | Professional-grade products |
These "molecular sponges" actively adsorb residual gases left after initial evacuation and continue working throughout the product's lifespan. At Cupique, we strategically place these getters to ensure maximum effectiveness and longevity.
Proper outgassing through high-temperature baking is critical for superior vacuum insulation.True
The passage states that proper outgassing through high-temperature baking is one of the four critical elements for achieving superior vacuum insulation.
Initial thermal tests are the only factor that matters for vacuum insulation performance.False
The passage states that initial thermal tests are not the only factor, and that true performance is revealed months after purchase when inferior products start failing.
What are the most common manufacturing pitfalls that compromise vacuum integrity, and how can B2B buyers identify them
I've seen countless samples from competitors that looked perfect but failed within months. The reason? Hidden manufacturing shortcuts that aren't visible to the naked eye but devastate performance over time.
Common vacuum integrity pitfalls include achieving only a "soft vacuum" during production, contamination of the vacuum cavity with particles or moisture, weld defects in critical seams, and improper getter material management. B2B buyers should request specific vacuum level targets, inspect production environments, and examine quality control protocols.
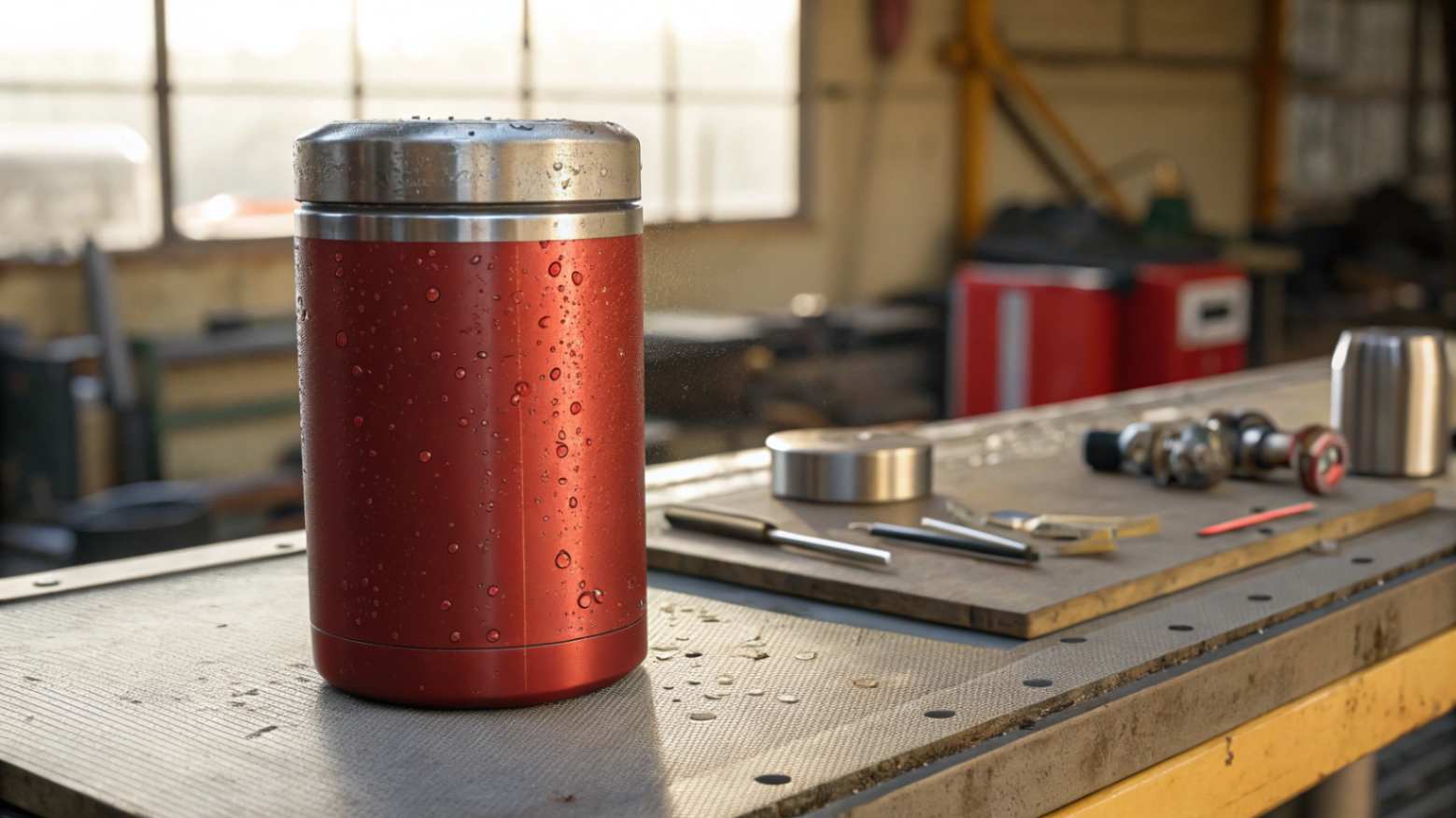
The "Phantom Vacuum" Problem
The most prevalent issue in the industry is what I call the "phantom vacuum" - bottles that technically have a vacuum but at insufficient levels for proper insulation. This occurs when:
- Manufacturers use inadequate pumping capacity
- Production lines move too quickly, allowing insufficient pump-down time
- Vacuum gauges are poorly calibrated or infrequently verified
At Cupique, we target vacuum levels below 0.1 Pa, while many competitors settle for 1-10 Pa (a 10-100x difference). This seemingly small difference dramatically impacts performance, especially over time.
Identifying Quality Through Manufacturing Environment
When I visit potential manufacturing partners, I immediately assess their vacuum production environment. Key indicators of quality include:
Quality Indicator | What to Look For | Red Flags |
---|---|---|
Assembly Environment | Clean room or controlled area | Dusty, oily surroundings |
Component Handling | Gloves, systematic procedures | Bare hands, casual handling |
Pre-Welding Storage | Sealed containers, climate control | Open air storage, visible dust |
Vacuum Equipment | Modern, well-maintained pumps | Outdated, leaking systems |
Testing Procedures | Documented protocols, data logging | Subjective "feel tests" only |
Weld Quality: The Critical Failure Point
The circumferential welds joining the inner and outer shells, along with the final vacuum port seal, represent the most vulnerable points for vacuum failure. Quality manufacturers employ:
- Advanced Welding Techniques: Laser or electron beam welding for critical seams
- Comprehensive Inspection: Visual checks under magnification, plus sampling for destructive testing
- Stress Testing: Thermal cycling tests to simulate years of use in accelerated conditions
At Cupique, we've invested in automated weld inspection systems that can detect microscopic imperfections invisible to the human eye, ensuring consistent quality across millions of units annually.
Which innovations in vacuum technology are genuinely impacting thermal performance, durability, and production efficiency for B2B sourcing
In my years attending industry trade shows, I've seen countless "innovations" that were merely marketing gimmicks. However, several genuine technological advances are transforming our industry in meaningful ways.
Genuine vacuum technology innovations include tailless vacuum welding that eliminates vulnerable evacuation ports, advanced getter formulations that extend performance life, automated in-line vacuum testing for 100% quality verification, and enhanced reflective layers that significantly reduce radiative heat transfer for superior insulation.
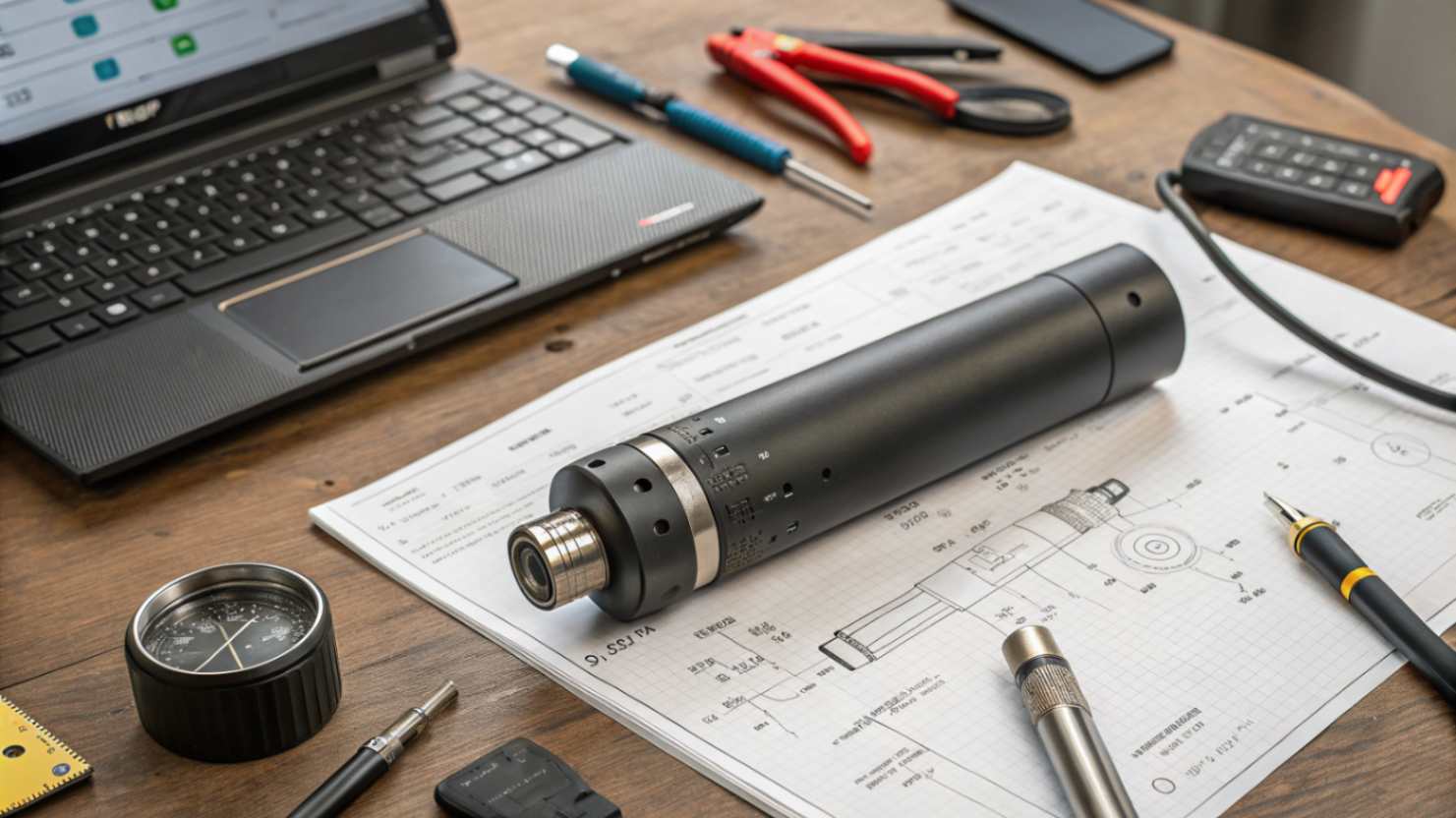
Tailless Vacuum Technology: A Game-Changer for Durability
Traditional vacuum bottles have a small "tail" or evacuation port at the bottom—a vulnerable point for vacuum loss and physical damage. The tailless vacuum technology we've implemented at Cupique represents a significant advancement:
How Tailless Technology Works
The process occurs entirely within a vacuum chamber, where:
- The complete bottle assembly is placed inside a specialized vacuum furnace
- The entire chamber is evacuated to the target vacuum level
- A precisely controlled brazing or welding process seals the unit while still under vacuum
- The result is a seamless bottom with no evacuation port
This technology not only improves aesthetics but significantly enhances durability and reduces failure rates. Our investment in this technology has reduced warranty claims by over 40% compared to our previous generation products.
Data-Driven Manufacturing: The Future of Quality Control
Perhaps the most impactful innovation for B2B buyers is the integration of data analytics into vacuum insulation manufacturing:
Innovation | Traditional Approach | New Data-Driven Approach | Business Impact |
---|---|---|---|
Vacuum Testing | Batch sampling (e.g., 1%) | 100% in-line testing | Elimination of "bad batches" |
Performance Tracking | Pass/fail only | Quantitative measurement | Predictive quality models |
Process Control | Manual adjustments | Automated feedback loops | Consistent quality across production runs |
Traceability | Limited batch records | Complete digital history | Rapid issue identification and resolution |
At Cupique, we've implemented these systems across our two production lines, including one fully automated lines. This allows us to provide our B2B partners with detailed quality documentation and consistent performance across millions of units annually.
Vacuum innovations improve thermal performance, durability, and production efficiencyTrue
The paragraph describes several genuine vacuum technology innovations that enhance these key metrics.
Vacuum innovations are mostly marketing gimmicksFalse
The paragraph explicitly states that some innovations are genuine and transforming the industry.
Beyond simply asking "do you vacuum test?", what critical questions about the vacuum process should B2B buyers ask potential suppliers to ensure quality and reliability
After working with hundreds of B2B clients, I've noticed that even experienced buyers often don't know the right questions to ask. This knowledge gap can lead to disappointing products and damaged customer relationships.
B2B buyers should ask suppliers about specific vacuum level targets and aging period tests, outgassing processes for components, getter material specifications, weld seam quality control methods, typical failure rates with root causes, and consistency of vacuum space geometry. These technical questions quickly separate premium manufacturers from those cutting corners.

Beyond Surface-Level Questions
When I consult with our B2B partners, I recommend they probe deeper with these specific questions:
Technical Specifications to Request
Rather than asking general questions, request specific technical parameters:
- Target Vacuum Level: "What is your target vacuum level in Pascals, and what maximum reading is acceptable for a passed unit after a 24-hour aging period?"
- Outgassing Protocol: "Describe your outgassing process for the shells prior to vacuumization – specifically temperature, duration, and vacuum level during baking."
- Getter Specifications: "What type of getter material do you use, and what is your rationale for its selection and placement?"
Quality Control Transparency
A manufacturer confident in their processes will readily share:
Quality Aspect | What to Ask | What to Look For in the Answer |
---|---|---|
Weld Integrity | "What specific checks are performed on weld seams?" | Mention of visual inspection under magnification, dye penetrant testing, or destructive testing |
Failure Rates | "What percentage of production typically fails vacuum tests?" | Realistic figures (0% is suspicious) and knowledge of root causes |
Long-term Testing | "Do you perform accelerated life testing?" | Evidence of thermal cycling tests and long-term performance data |
Dimensional Control | "How do you ensure consistency of the vacuum space volume?" | References to specific measurement techniques and tolerances |
At Cupique, we provide our B2B partners with comprehensive technical documentation covering all these aspects. This transparency has been key to building long-term relationships with retailers and distributors across Europe, North America, Australia, and Southeast Asia.
The Value of Factory Visits
While documentation is important, nothing replaces seeing the production process firsthand. During factory visits to our 30,000 square meter facility, we encourage clients to:
- Observe the cleanliness of pre-vacuum assembly areas
- Review our vacuum testing data logs
- Witness our quality control procedures in action
- Examine samples from our accelerated aging tests
These visits consistently demonstrate the difference between marketing claims and actual manufacturing excellence.
B2B buyers should ask suppliers about specific technical details of their vacuum processTrue
The passage states that buyers should ask about vacuum level targets, outgassing, weld quality, and other technical aspects to assess quality.
B2B buyers only need to ask if suppliers do vacuum testingFalse
The passage states that simply asking about vacuum testing is not enough, and buyers should ask more specific technical questions.
Conclusion
Superior vacuum insulation in stainless steel bottles comes down to meticulous manufacturing processes, not marketing claims. By understanding the critical factors of surface preparation, proper vacuum levels, getter materials, and seal integrity, B2B buyers can select suppliers who deliver products that truly perform.