To fix a leaking stainless steel water bottle, first identify the leak source - typically the lid seal, threading, or rarely the bottle body itself. For lid leaks, replace the silicone gasket or O-ring. For thread issues, ensure proper alignment when closing. Bottom leaks indicate manufacturing defects requiring professional repair or replacement.
When I first started manufacturing stainless steel bottles at Cupique, leak prevention became our top priority. Our research showed that leakage was the number one reason for customer returns. Let me share what we've learned about fixing, preventing, and addressing leaks from a manufacturer's perspective.
Lid seals and threading are common leak sources in stainless steel water bottles.True
The paragraph states that lid seals and threading are typical sources of leaks in stainless steel water bottles.
Leaking stainless steel water bottles are always due to manufacturing defects.False
The paragraph indicates that while bottom leaks may indicate manufacturing defects, lid seals and threading issues are more common leak sources.
How do you seal a leaking water bottle
Customers often contact us about leaking bottles, frustrated with wet bags and damaged electronics. I understand their pain - a leaking bottle can ruin someone's day and their trust in your brand.
To seal a leaking water bottle, first determine the leak source. For lid leaks, replace the silicone gasket or O-ring with a properly sized, food-grade replacement. For thread leaks, ensure proper alignment when closing and check for damage. Apply food-grade silicone grease to gaskets to extend their lifespan.
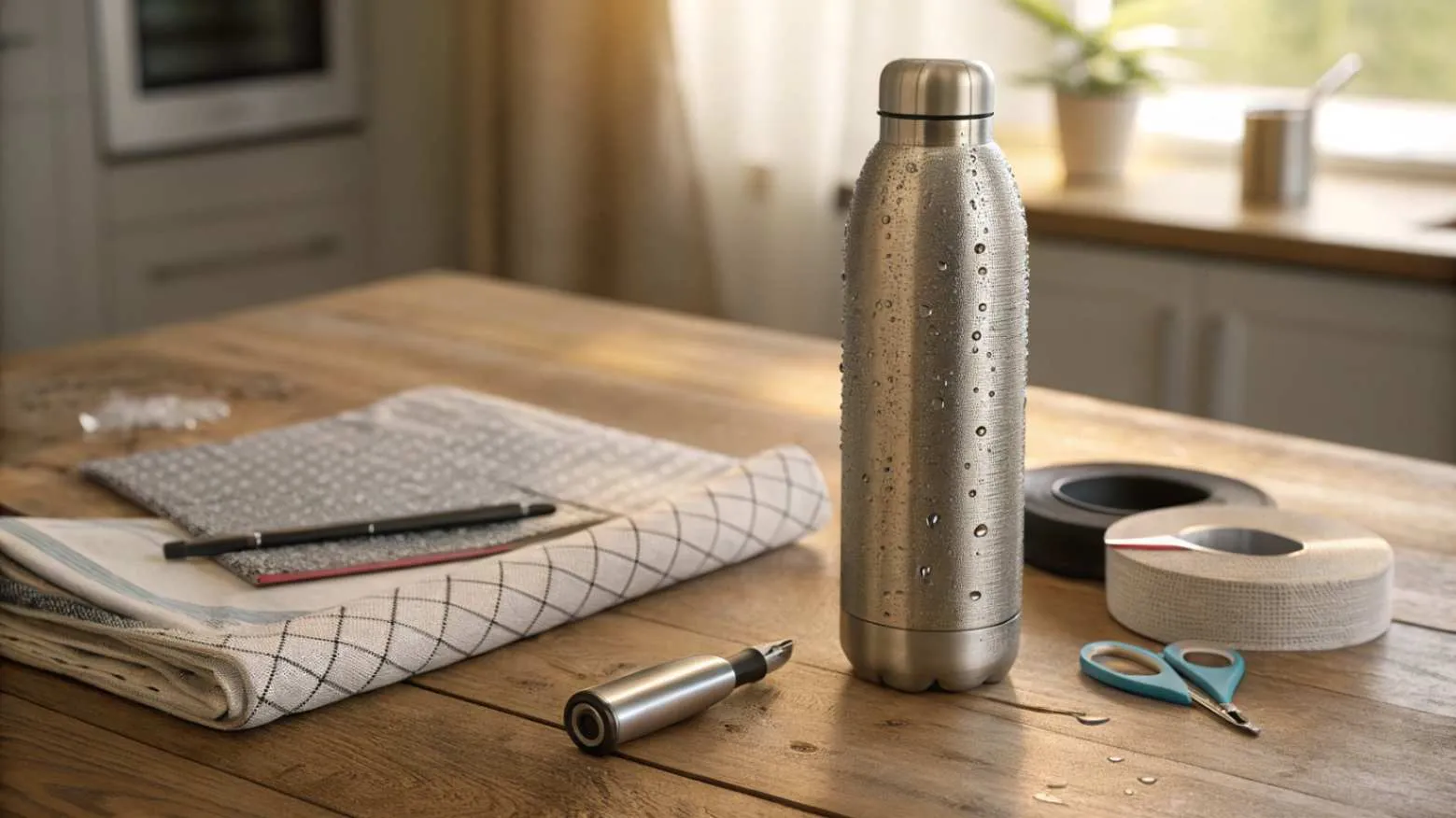
Understanding Leak Sources
The first step in fixing any leak is identifying its source. In our decade of manufacturing experience, we've found leaks typically originate from three main areas:
Leak Location | Common Causes | Detection Method | Fix Approach |
---|---|---|---|
Lid/Cap | Worn gasket, damaged threads, improper closure | Fill with water, close tightly, invert | Replace gasket, check thread alignment |
Bottle Body | Dents affecting seal surface, hairline cracks | Visual inspection, pressure test | Usually requires replacement |
Bottom Weld | Manufacturing defect, severe impact | Water test on flat surface | Manufacturing issue - replacement needed |
Gasket Replacement Technique
For lid leaks, which account for approximately 85% of all leakage issues, the solution often involves the gasket. At Cupique, we've developed a specific gasket replacement protocol:
- Remove the existing gasket carefully using a non-metal tool
- Clean the gasket groove thoroughly
- Install a new gasket of identical specifications
- Apply light food-grade silicone lubricant to extend lifespan
This simple procedure resolves most leakage issues and is something we train our B2B partners to communicate to their customers.
Replacing the silicone gasket or O-ring can seal lid leaks.True
The snippet paragraph states that for lid leaks, replacing the silicone gasket or O-ring with a properly sized, food-grade replacement can help seal the leak.
Applying superglue to the threads can seal thread leaks.False
The snippet paragraph recommends ensuring proper alignment when closing the bottle and checking for damage, not applying superglue to the threads, to seal thread leaks.
What makes a water bottle leak proof
Every time we develop a new bottle design, leak-proof performance is our top priority. I've rejected countless prototypes that didn't meet our stringent standards for seal integrity.
A truly leak-proof water bottle combines precision-engineered threading, high-quality silicone gaskets with optimal compression ratios, and flawless welding of the stainless steel body. The lid design should create multiple sealing points, and quality control must include pressure testing of each unit.
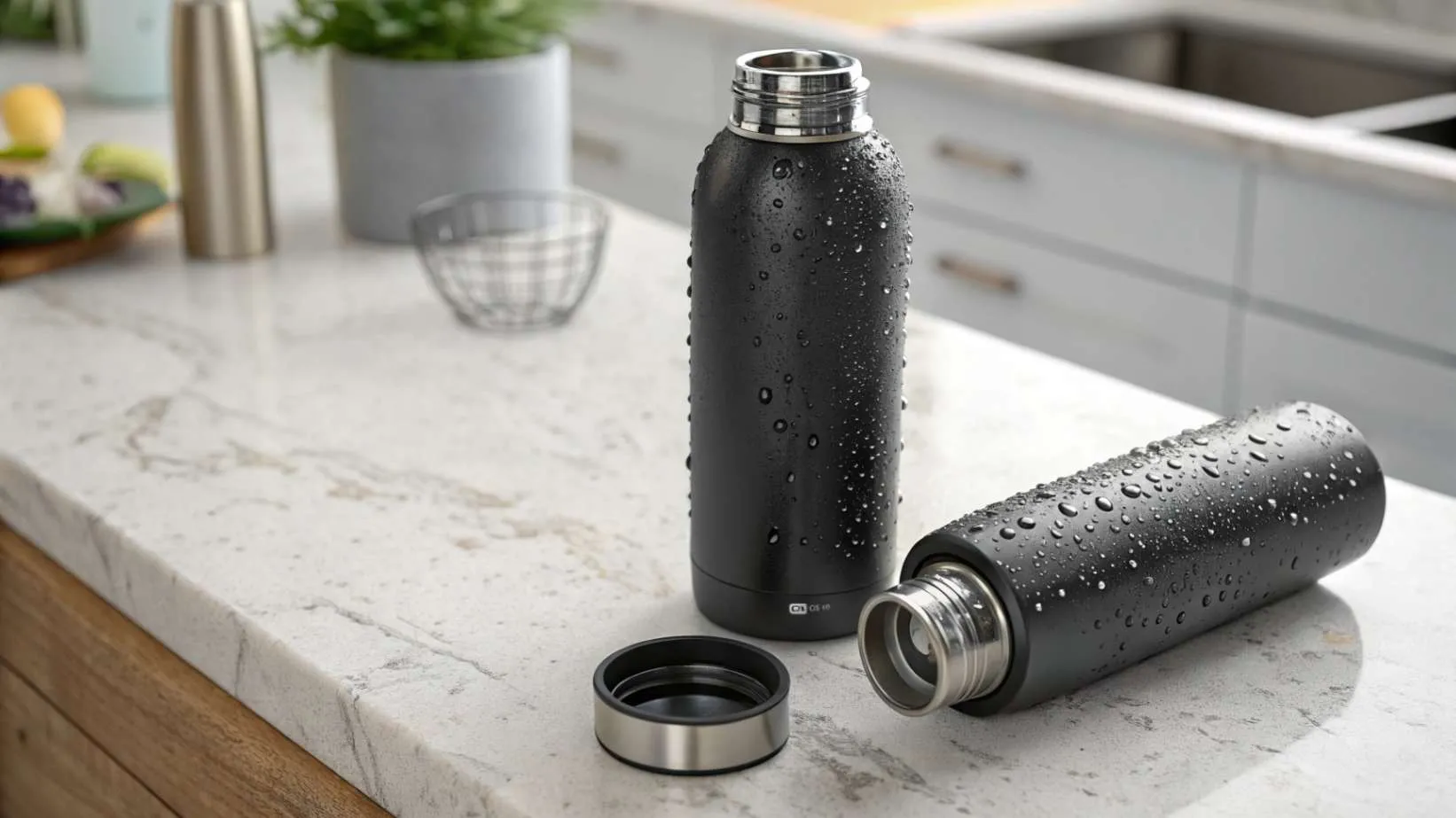
Engineering Leak-Proof Performance
Creating a genuinely leak-proof bottle begins long before manufacturing. In our Cupique factory, we've identified critical factors that determine leak resistance:
Material Selection Criteria
The materials used in sealing components dramatically impact performance. Our testing has shown:
Component | Optimal Material | Key Properties | Common Failures |
---|---|---|---|
Gasket/O-ring | Food-grade silicone (40-60 durometer) | Compression set resistance, temperature stability | Hardening, deformation, tearing |
Bottle Body | 304/316 stainless steel (0.6-0.8mm thickness) | Corrosion resistance, impact resistance | Weld failures, denting at seal surfaces |
Lid Threading | Polypropylene or stainless steel | Precision tolerance, wear resistance | Thread stripping, uneven wear |
Critical Design Elements
Beyond materials, specific design elements contribute to leak-proof performance. Our engineering team focuses on:
- Thread Engagement Depth - Minimum 2.5 turns for secure closure
- Gasket Compression Ratio - Typically 20-30% for optimal sealing without excessive wear
- Pressure Relief Mechanisms - Preventing internal pressure buildup that can force liquid past seals
- Impact-Resistant Zones - Reinforced areas around sealing surfaces
These design considerations are what separate premium bottles from those that will inevitably leak. When evaluating suppliers, B2B buyers should request detailed specifications on these elements rather than simply accepting "leak-proof" claims.
Leak-proof water bottles require precise engineering and quality controlTrue
The passage emphasizes the importance of precision engineering, quality gaskets, and pressure testing to ensure leak-proof performance.
Water bottle lids only need a single sealing point to be leak-proofFalse
The passage states that the lid design should create multiple sealing points for a truly leak-proof bottle.
How do you protect a stainless steel water bottle
In our customer education materials, we emphasize proper care. I've seen perfectly manufactured bottles develop leaks simply due to improper handling or maintenance.
Protect stainless steel water bottles by avoiding drops that can damage sealing surfaces, preventing extreme temperature changes that stress materials, cleaning threads and gaskets gently, storing with lids off to prevent gasket compression, and using protective silicone boots for active lifestyles.

Comprehensive Protection Strategies
Protection extends beyond just preventing physical damage. At Cupique, we recommend a holistic approach to bottle care:
Physical Protection Systems
For B2B clients targeting active users, we offer various protection options:
Protection Type | Benefits | Best Applications |
---|---|---|
Silicone Bottom Boots | Prevents base denting, improves stability | Outdoor, sports, travel |
Full Silicone Sleeves | Impact absorption, improved grip | Gym, children's bottles |
Reinforced Carrying Loops | Reduces drop risk | Hiking, commuting |
Protective Caps | Keeps drinking surfaces clean | Outdoor activities |
Maintenance Protocols for Extended Seal Life
Proper maintenance significantly extends the functional life of sealing components:
- Regular Inspection - Check gaskets monthly for signs of wear or deformation
- Proper Cleaning - Use soft brushes for threads, avoid abrasives on sealing surfaces
- Correct Storage - Store with lid loosely attached to prevent gasket compression set
- Temperature Management - Avoid extreme temperature changes that can stress materials
Material Compatibility Considerations
Not all cleaning agents are safe for bottle components:
Cleaning Agent | Effect on Components | Recommendation |
---|---|---|
Vinegar Solutions | Safe for steel, may degrade some gaskets | Use diluted, rinse thoroughly |
Bleach | Can damage gaskets, safe for steel in low concentrations | Avoid or use very diluted |
Dishwasher Detergents | May accelerate gasket wear | Hand wash recommended for premium bottles |
By educating end-users on these protection strategies, B2B buyers can significantly reduce warranty claims and improve customer satisfaction.
Proper handling and maintenance are key to preventing leaks in stainless steel water bottlesTrue
The passage highlights the importance of proper care to avoid damage and leaks in stainless steel water bottles.
Stainless steel water bottles are indestructible and do not require any special careFalse
The passage indicates that even well-manufactured bottles can develop leaks due to improper handling or maintenance.
How to fix a leaking water bottle from the bottom
Bottom leaks are particularly concerning as they indicate fundamental manufacturing issues. I take these reports very seriously as they often reveal process improvements needed in our production line.
A water bottle leaking from the bottom typically indicates a manufacturing defect in the base weld. This is not repairable by end-users and requires replacement. For B2B buyers, this signals the need for supplier quality review, as bottom leaks indicate failures in welding processes or inspection protocols.
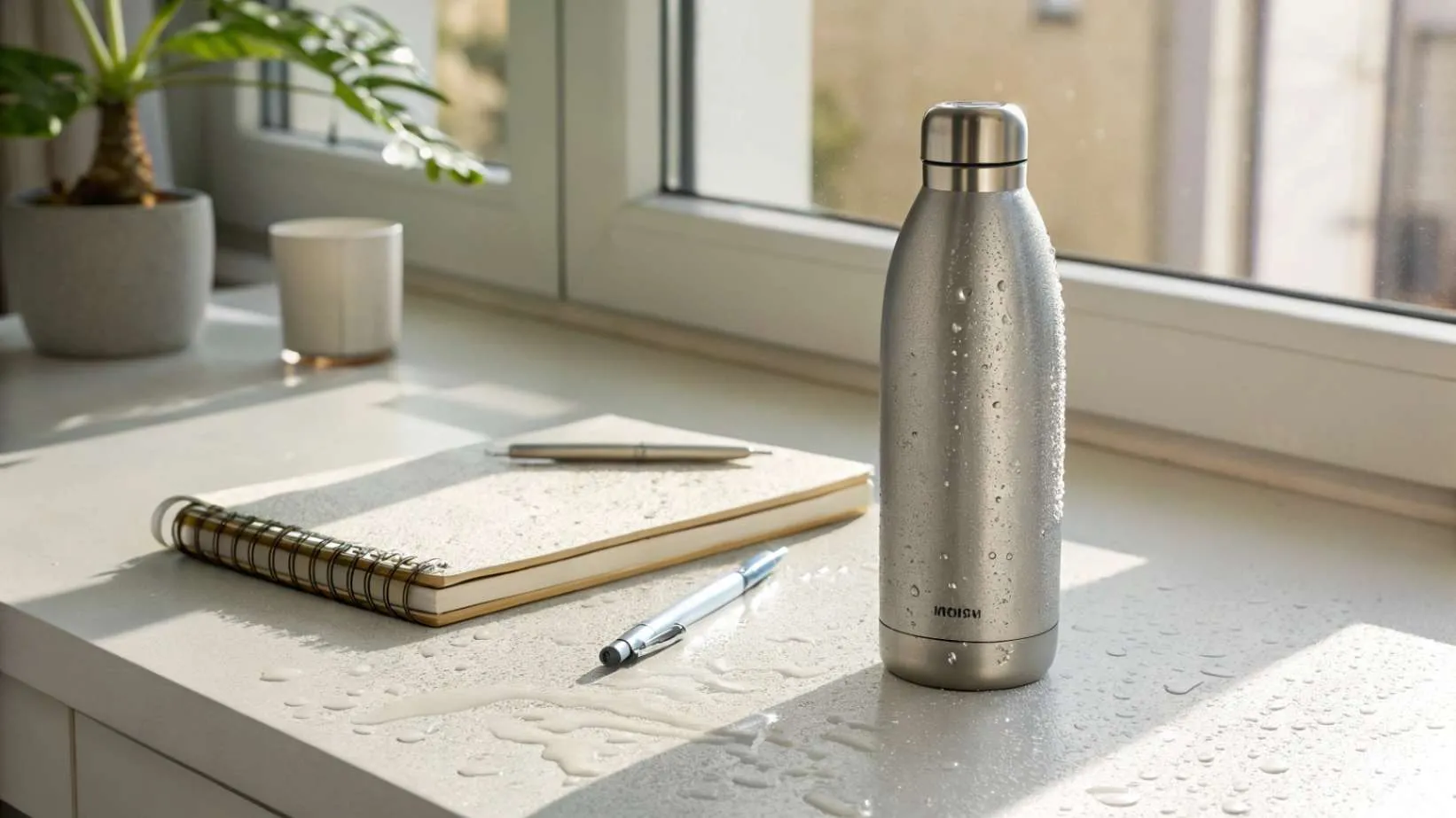
Manufacturing Implications of Bottom Leaks
When a bottle leaks from the bottom, it reveals critical information about production quality:
Root Cause Analysis
At Cupique, we've developed a systematic approach to bottom leak investigation:
Leak Pattern | Likely Cause | Manufacturing Process Implicated | Corrective Action |
---|---|---|---|
Pinhole Leaks | Material defects or incomplete weld penetration | Material sourcing or welding parameters | Supplier audit, welding parameter adjustment |
Seam Leaks | Improper weld setup or post-weld stress | Welding fixture alignment or handling procedures | Fixture recalibration, process review |
General Seepage | Micro-fractures from impact during production | Material handling or packaging | Process audit, packaging redesign |
Quality Control Protocols
To prevent bottom leaks from reaching customers, we implement:
- 100% Air Pressure Testing - Each bottle is pressurized and submerged to detect even microscopic leaks
- Weld X-ray Sampling - Random samples undergo X-ray inspection to verify weld integrity
- Drop Testing - Sample testing to ensure welds withstand impact
B2B Buyer Protection Strategies
For B2B buyers sourcing stainless steel bottles, I recommend these protective measures:
- Request Testing Documentation - Suppliers should provide detailed testing protocols and results
- Sample Testing - Conduct independent testing on initial samples before bulk orders
- Clear Warranty Terms - Establish explicit terms covering manufacturing defects
- Batch Traceability - Ensure each production run is traceable for quality control purposes
Bottom leaks, unlike lid leaks, cannot be addressed with simple fixes. They require a systematic approach to quality control and supplier management. By implementing these strategies, B2B buyers can significantly reduce the risk of receiving defective products.
Bottom leaks in water bottles indicate manufacturing defectsTrue
The snippet paragraph explains that bottom leaks are caused by issues in the base weld or production process.
Bottom leaks in water bottles can be repaired by end-usersFalse
The snippet states that bottom leaks are not repairable by end-users and require replacement.
Conclusion
Preventing and addressing leaks in stainless steel water bottles requires attention to design, materials, manufacturing, and user education. By understanding these factors, B2B buyers can select quality suppliers and provide valuable guidance to their customers.